Principles of Operation
The spray header delivers the sump solution to the top of the packed bed section of the Scrubber. Carefully chosen nozzles, along with select placement, distribute the full flow as uniformly as possible. Temperature, pressure, and chemical compatibility help determine materials of construction (PVC, CPVC, PP, PVDF, SS, etc). See full cone spray pattern below.
The process vapor to be treated, containing odors or chemical fumes, enter into the Scrubber's inlet transition. These gases may have positive pressure applied and pushed into the Scrubber (Forced Draft) or may be under negative pressure and sucked into the Scrubber (Induced Draft). A well design system will account for velocity and flow distribution on the inlet. Finally, it is typical that the incoming vapor stream's temperature is below 185F for FRP constructed Scrubbers.
The clean vapor stream exits the exhaust section of the Scrubber with the pollutants of concern removed down to requested emission limits. This cleaned vapor stream will be fully saturated with water (100% relative humidity). If the temperature of the vapor stream cools through additional ductwork, a stack, or as it exits into the atmosphere, water vapor will begin to condense out. That is why some exhaust stacks display a white water vapor cloud that quickly dissipates.
Packed bed Scrubbers (Chemical Scrubbers, Odor Scrubbers, Gas Scrubbers) are engineered for removal and / or neutralization of various odors and chemical fumes. They are commonly constructed from FRP (Fiberglass Reinforced Plastic).
The diameter of a Scrubber is a function of the incoming process vapor flowrate and the height of the Scrubber is related to the desired removal efficiency of the pollutants. Engineering calculations not only physically size the equipment, but also determine the operating parameters: liquid flowrate, pH/ORP setpoints, chemical reagent dosing, and wastewater blowdown.
The heart of the Scrubber is the packed bed section, which is randomly filled to a specified height (related to removal efficiency). Quality packing will provide high liquid dispersion, promote large surface areas, and have high void fractions. Large liquid surface areas (droplets and films) increases vapor to liquid interface, which improves scrubbing effectiveness. Large void fractions allow for increased vapor flowrates at lower pressure drops and also lower plugging concerns. Depending on the application, packing materials of construction may be PP, GFPP, PVDF, and SS.
The sump is a reservoir of liquid solution, which feeds the system pump. It is typically filled with water and then dosed with chemical reagents (i.e. NaOH - Caustic). Dosing may be controlled by a pH/ORP analyzer.
The sump solution will scrub the incoming dirty process vapor stream and entrain the resulting byproducts, typically a dissolved salt compound of the incoming pollutants. Over time, the solution becomes dirtier and more saturated with dissolved solids, which necessitates blowdown (discharge) to wastewater treatment. The rate or frequency of blowdown is dependent upon the incoming process vapor pollutant loadings. Larger amounts of pollutants, means quicker sump solution saturation.
Finally, the sump is very dynamic with water constantly being evaporated, solution being sent to blowdown, and make-up water solenoids turning on/off, along with turbulence, possible corrosive chemistries, foaming issues, or solids buildup. Therefore, to ensure proper operation of the sump and Scrubber, quality liquid level instrumentation is necessary.
The system pump is the muscle of the Scrubber and should be sized accordingly for full liquid flow and static pressures needed to recirculate the sump solution to the spray header. Temperature and densities of the liquid are important variables to consider. The pump's materials of construction must be able to handle the chemicals from the process vapor stream, any chemical reagent dosing, and any resulting chemical reaction byproducts. Wetted surfaces, gaskets, and seals must be compatible with all chemistries associated with the application.
The clean vapor stream passes through the mist eliminator as the final section of the Scrubber. A composite mesh pad is an example of a mist eliminator, comprised of interwoven fibers built up in coarse and fine layers. Water droplets that are carried upwards in the vapor stream from the spray header, are impacted on this mesh pad. The clean vapor stream passes through, whereas large water droplets are collected on the mesh pad and allowed to drain back down.
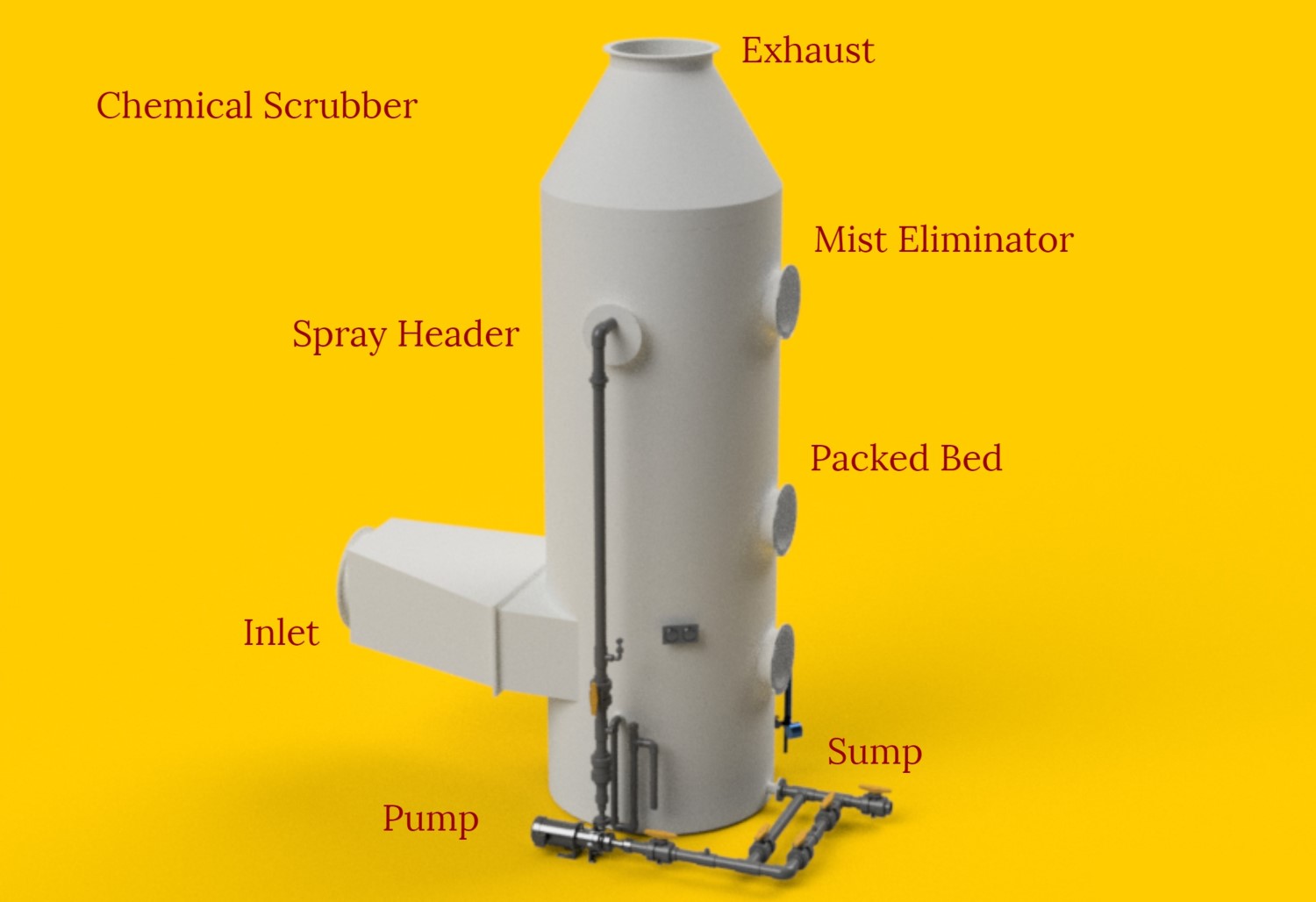
Common Pollutants
IDLH (Immediately Dangerous to Life or Health by NIOSH)
PEL (Permissable Exposure Limits by OSHA)
Odor Threshold data (Gregory Leonardos , David Kendall & Nancy Barnard (1969) Odor Threshold
Determinations of 53 Odorant Chemicals)
HYDROGEN CHLORIDE
(HCl)
Acidic
- IDLH: 50 ppm
- Odor Threshold: 10 ppm
- PEL: 5 ppm
Reagent: NaOH
Byproduct: Sodium Chloride – NaCl
ACETIC ACID
(C2H4O2)
Acidic
- IDLH: 50 ppm
- Odor Threshold: 1 ppm
- PEL: 10 ppm
Reagent: NaOH
Byproduct: Sodium Acetate – NaOAc
MERCAPTANS
(CH3SH)
Odorous
- IDLH: 150 ppm
- Odor Threshold: 2.1 ppb
- PEL: 10 ppm
Reagent: NaOH and NaOCl
Byproduct: Sodium Chloride – NaCl and Sodium Methanesulfonate – CH3SO3Na
HYDROGEN FLUORIDE
(HF)
Acidic
- IDLH: 30 ppm
- PEL: 3 ppm
- Very Corrosive
Reagent: NaOH
Byproduct: Sodium Fluoride – NaF
AMMONIA
(NH3)
Basic
- IDLH: 300 ppm
- Odor Threshold: 46.8 ppm
- PEL: 50 ppm
Reagent: Sulfuric Acid – H2SO4
Byproduct: Ammonium Sulfate – (NH4)2SO4
SULFUR DIOXIDE
(SO2)
Toxic
- IDLH: 100 ppm
- Odor Threshold: 0.47 ppm
- PEL: 5 ppm
Reagent: NaOH
Byproduct: Sodium Sulfite – Na2SO3 and Sodium Bisulfite – NaHSO3
CHLORINE
(Cl2)
Toxic
- IDLH: 10 ppm
- Odor Threshold: 0.314 ppm
- PEL: 1 ppm
Reagent: NaOH
Byproduct: Sodium Chloride – NaCl and Sodium Hypochlorite – NaOCl
FORMALDEHYDE
(CH2O)
Toxic
- IDLH: 20 ppm
- Odor Threshold: 1 ppm
- PEL: 0.75 ppm
Reagent: NaOH and Sodium Bisulfite – NaHSO3
Byproduct: Formaldehyde Bisulfite adduct – HOCH2SO3Na
HYDROGEN SULFIDE
(H2S)
Very Toxic
- IDLH: 100 ppm
- Odor Threshold: 0.47 ppb
- PEL: 10 ppm
Reagent: NaOH and NaOCl
Byproduct: Sodium Sulfate – Na2SO4 and Sodium Chloride – NaCl
ODORS
(Various)
Nuisance
- Wastewater fumes
- Pet Food Mfg
- H2S, Mercaptans
Reagent: NaOH and NaOCl (Sodium Hypochlorite) are commonly used
ETHYLENE OXIDE
(EO)
Carcinogen
- IDLH: 800 ppm
- PEL: 1 ppm
- Highly Flammable
Reagent: Sulfuric Acid – H2SO4
Byproduct: Ethylene Glycol – C2H6O2
Some Standard Sizes
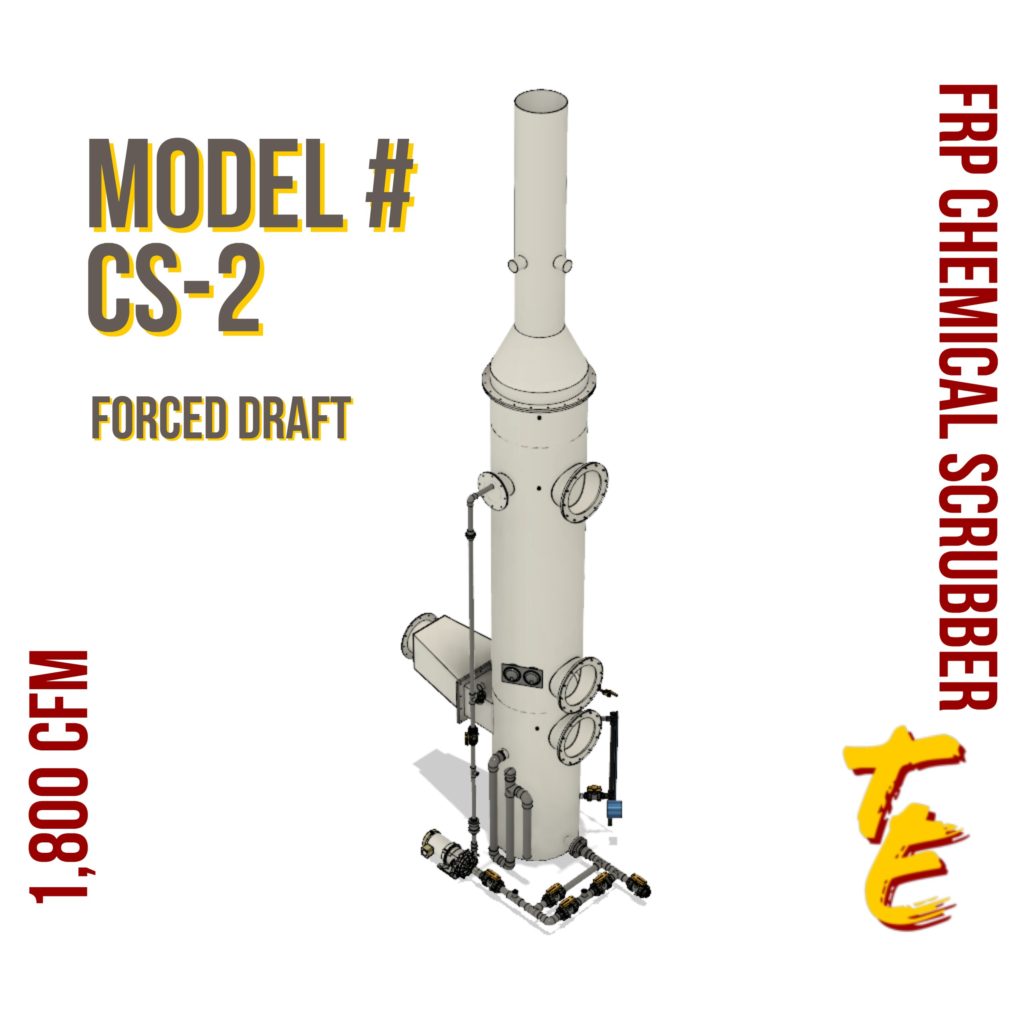
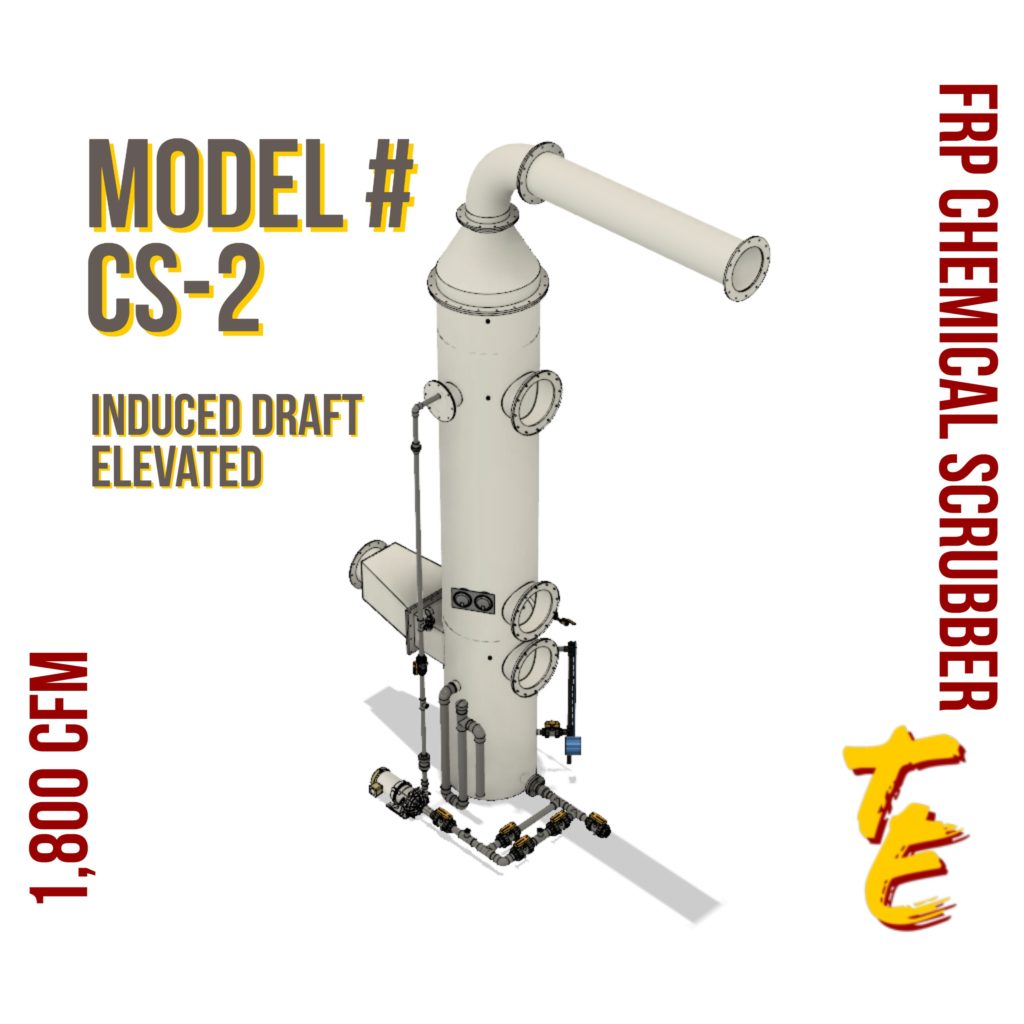
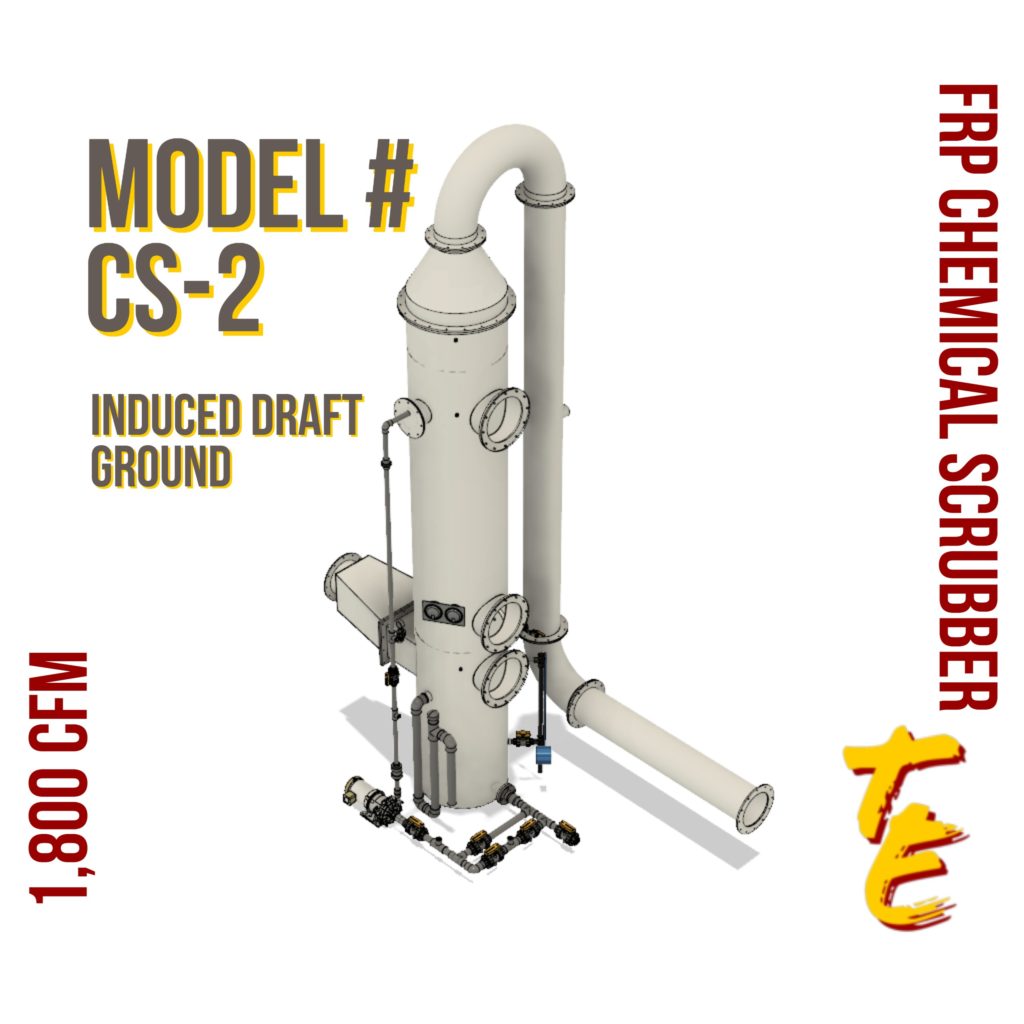
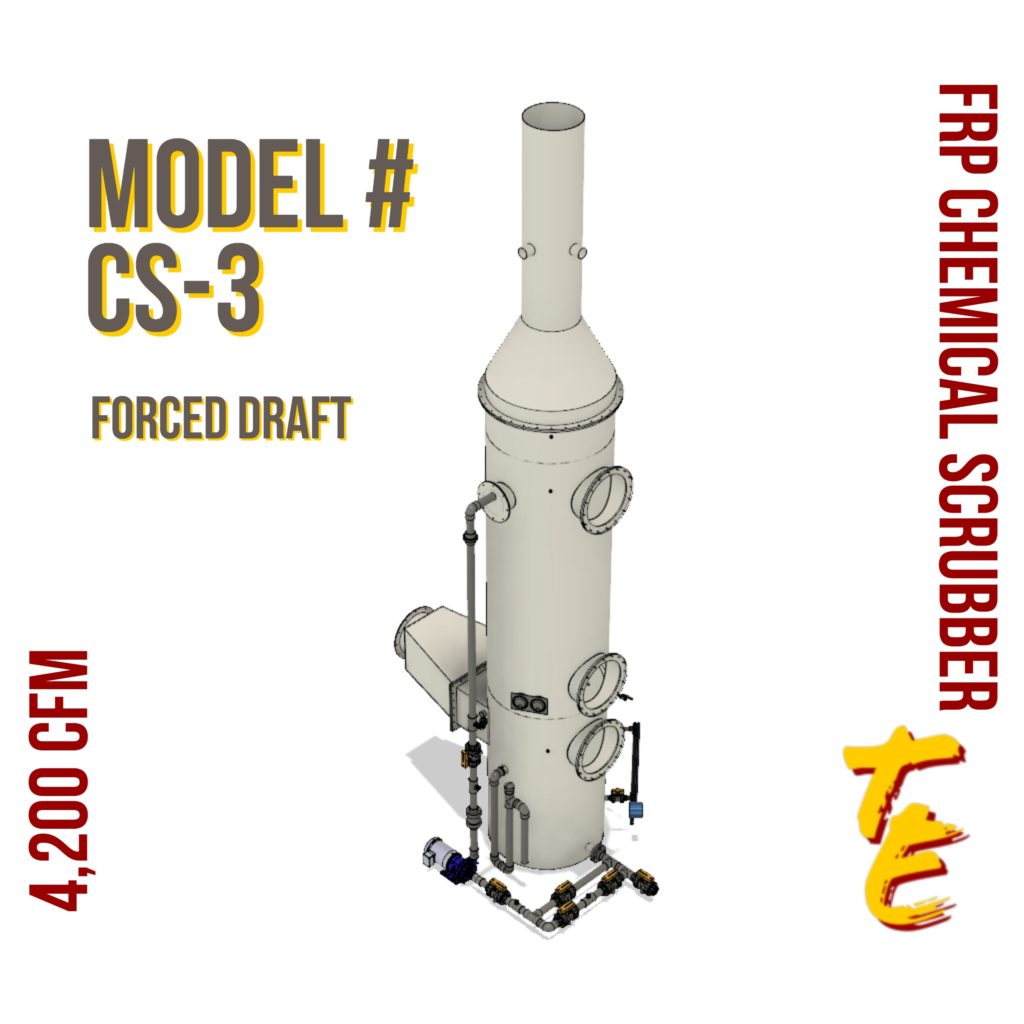
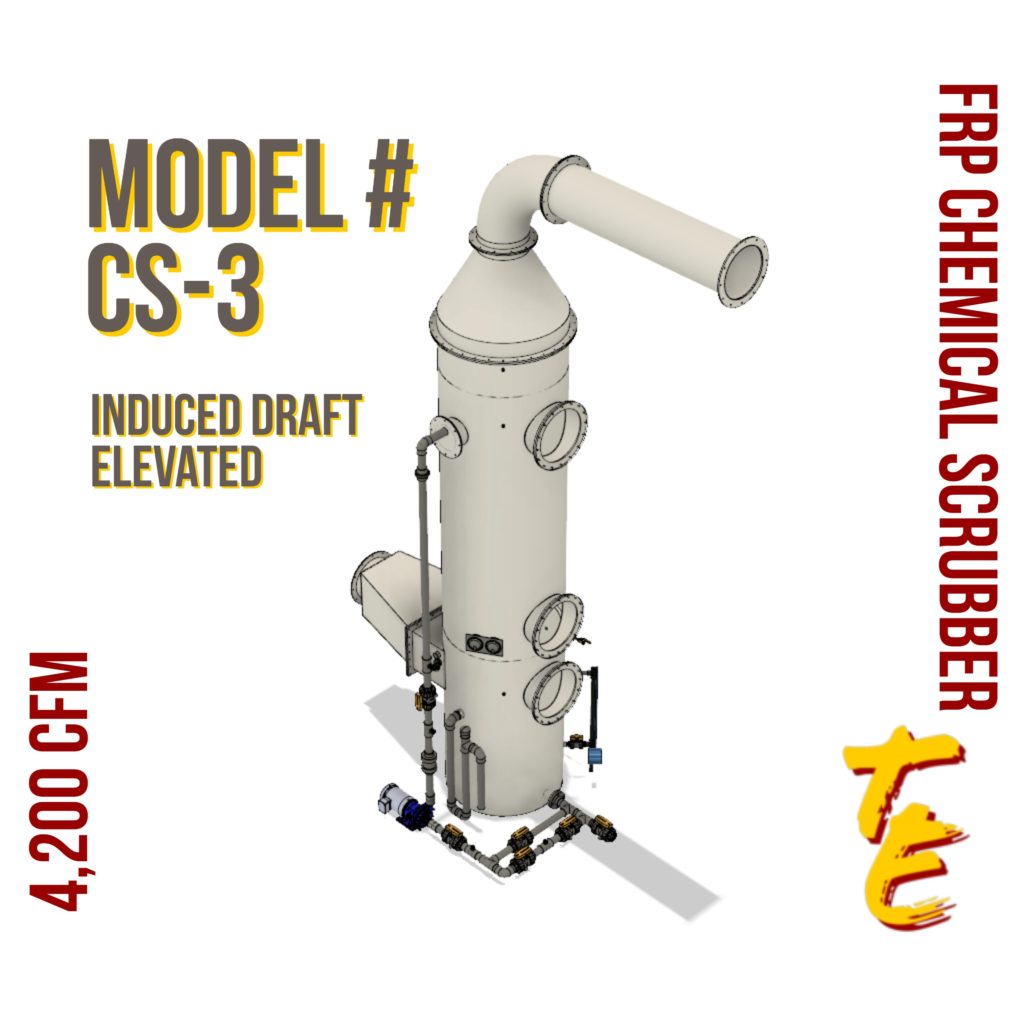
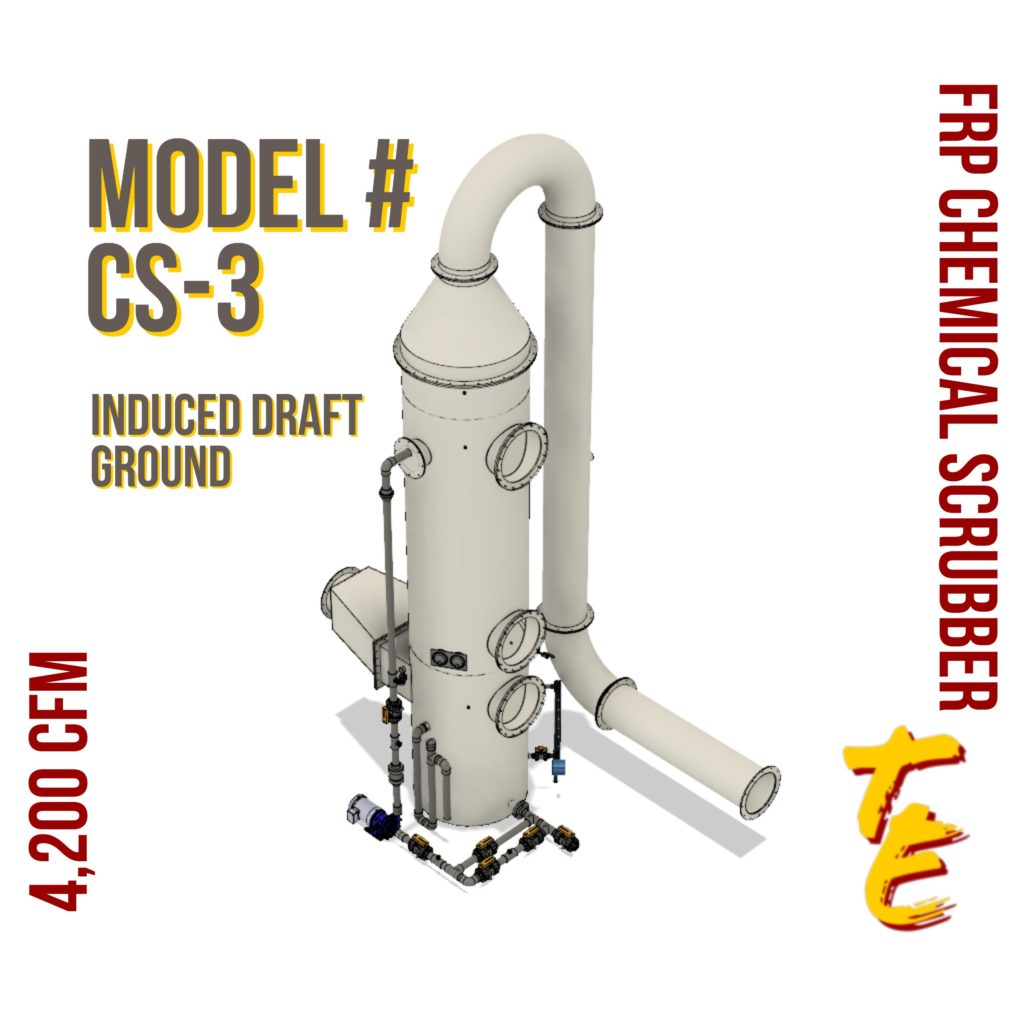
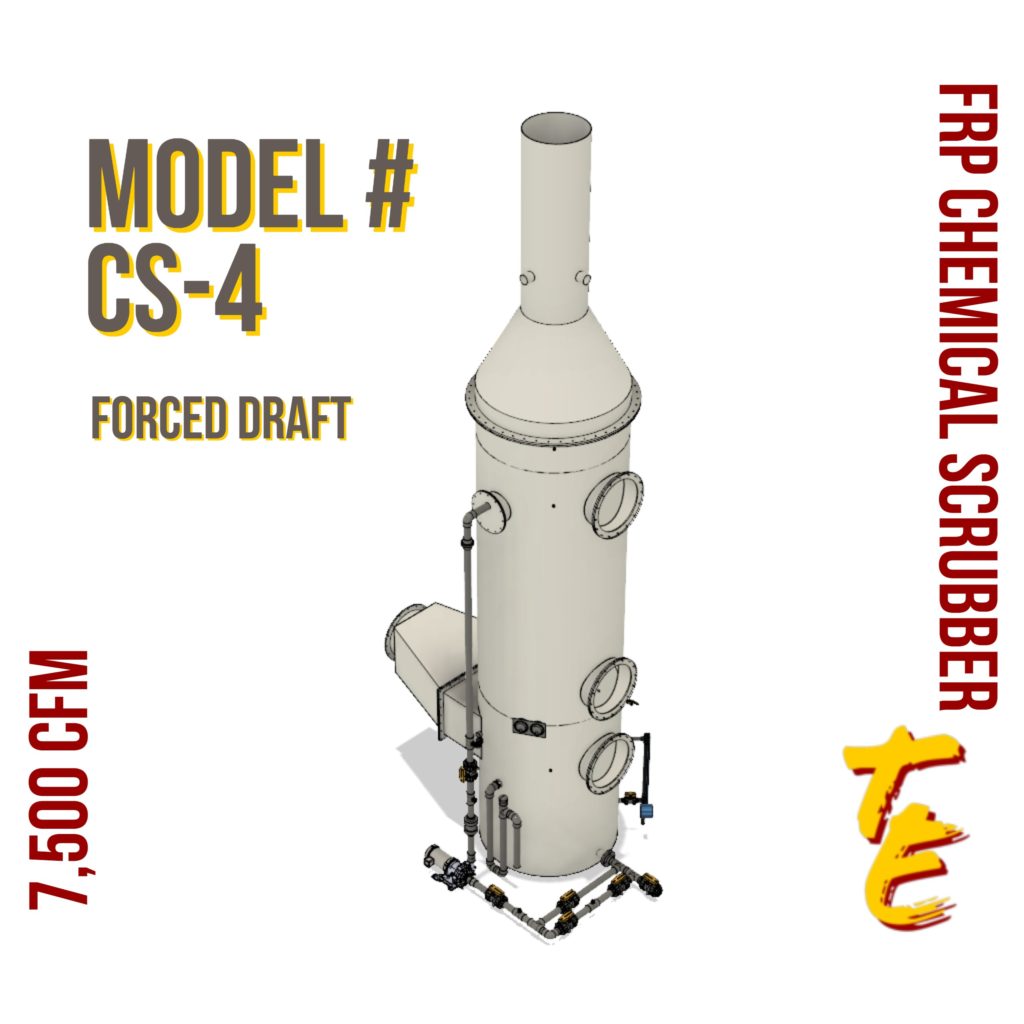
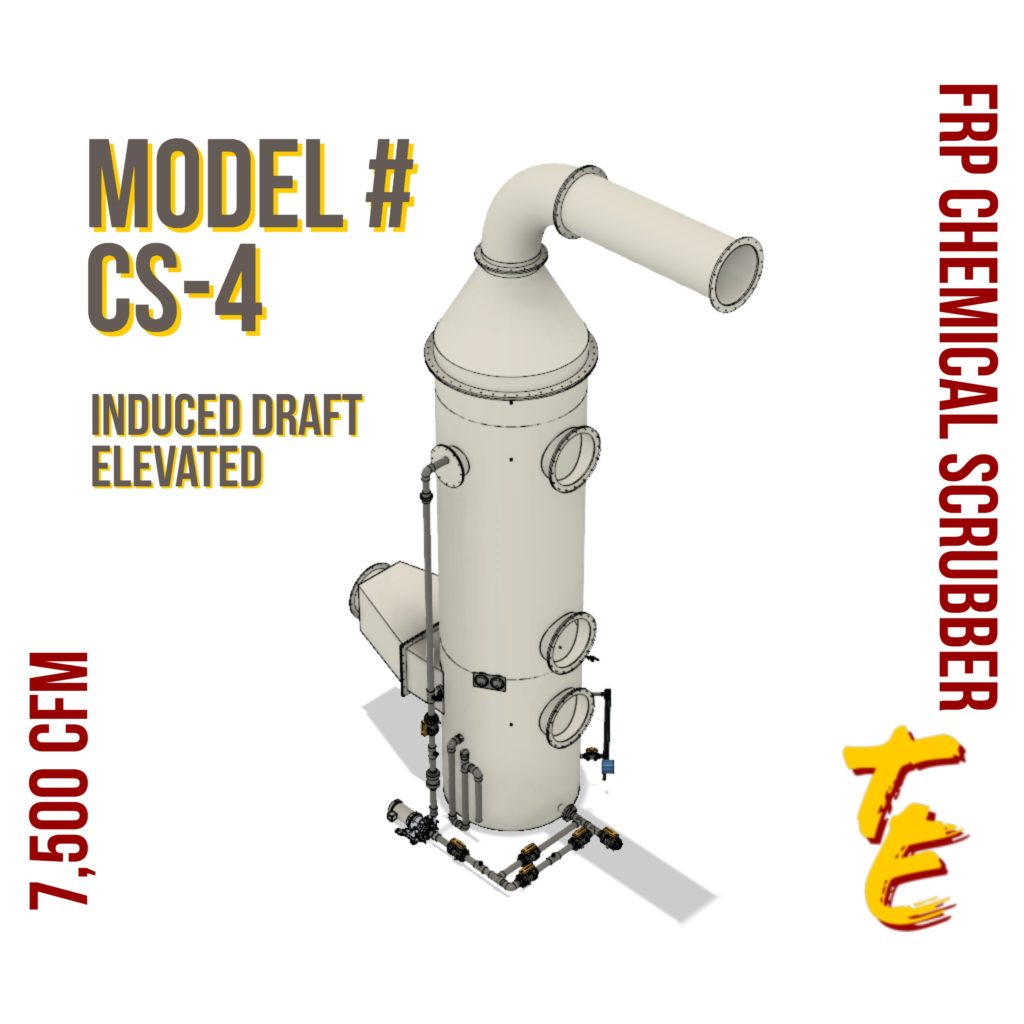
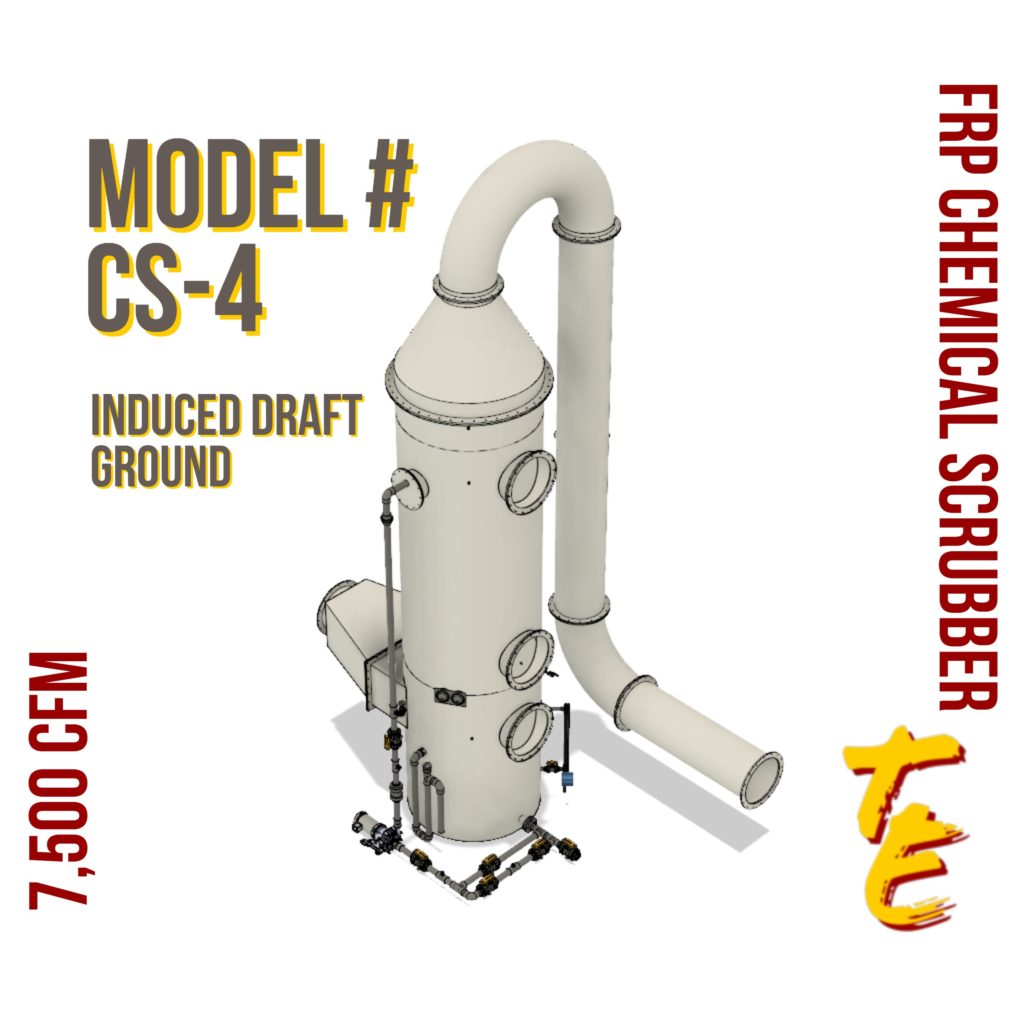
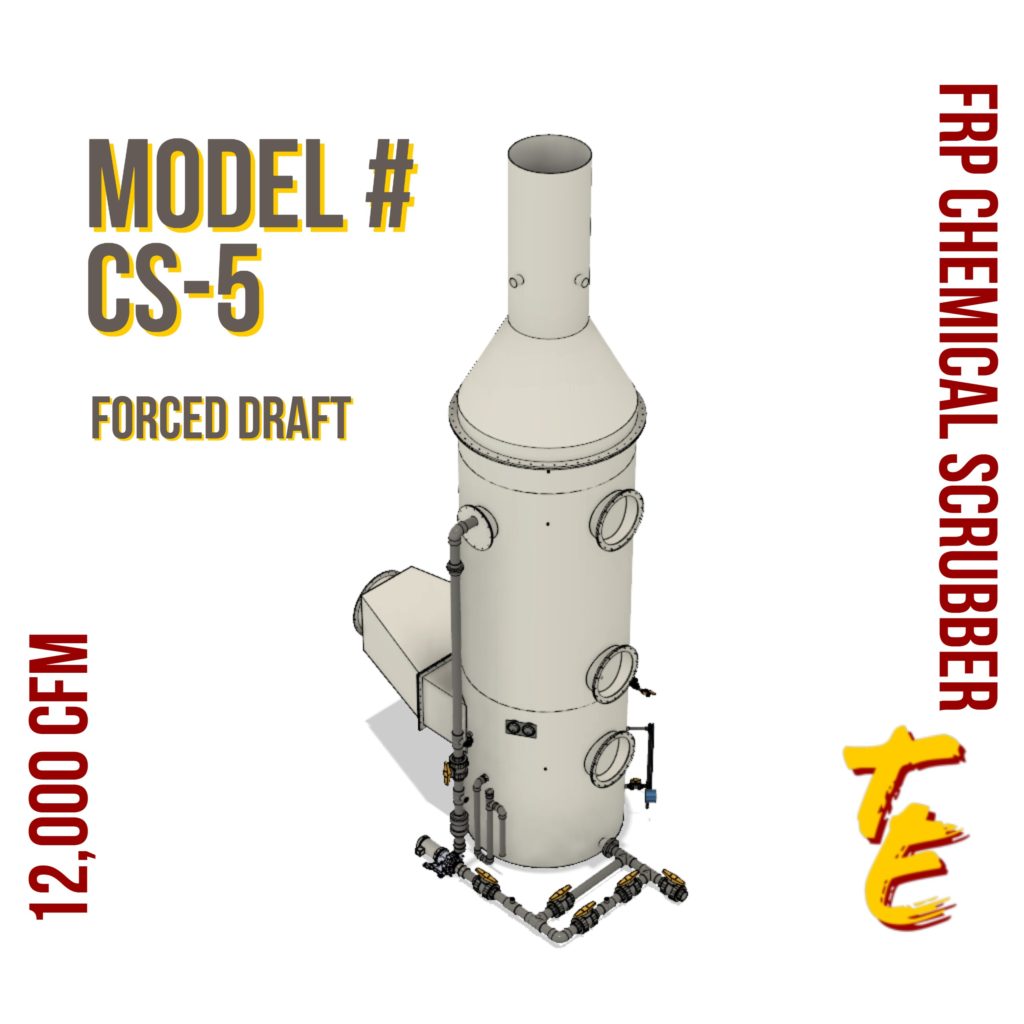
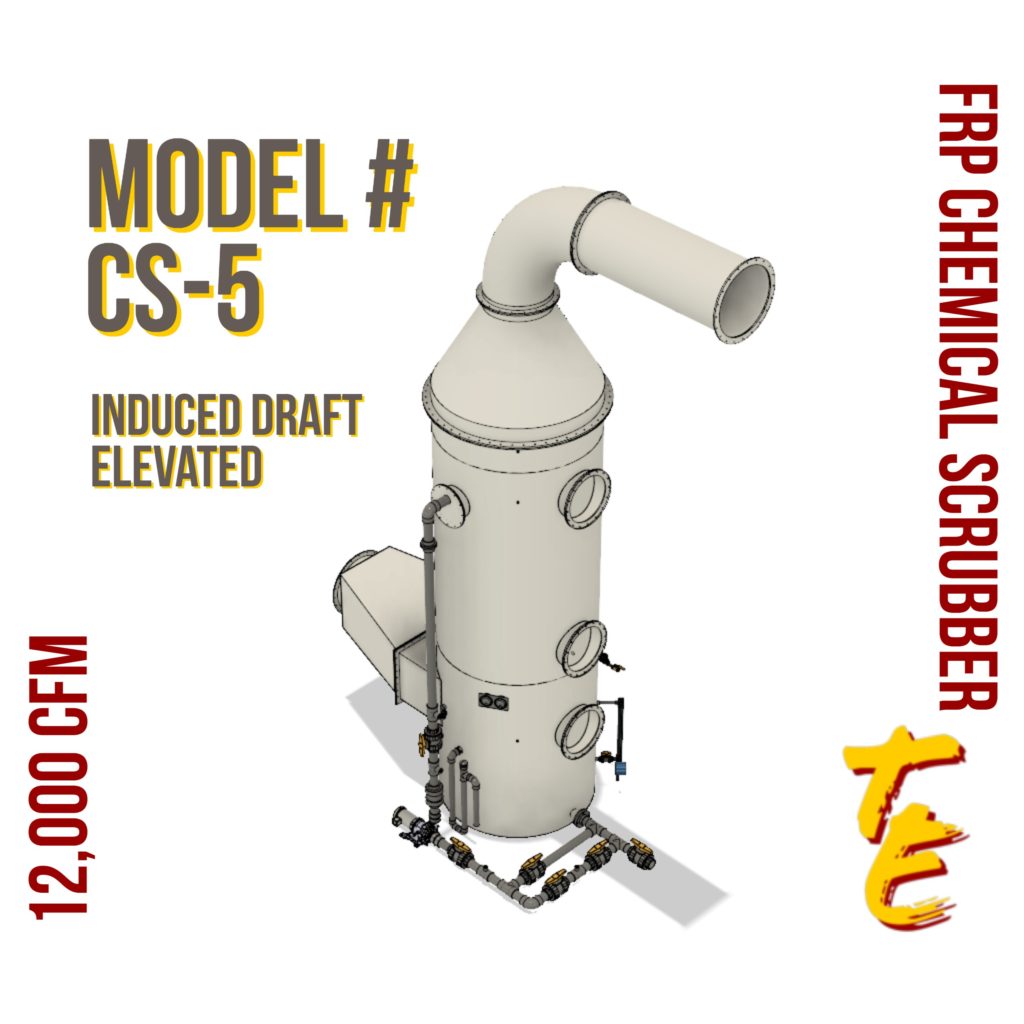
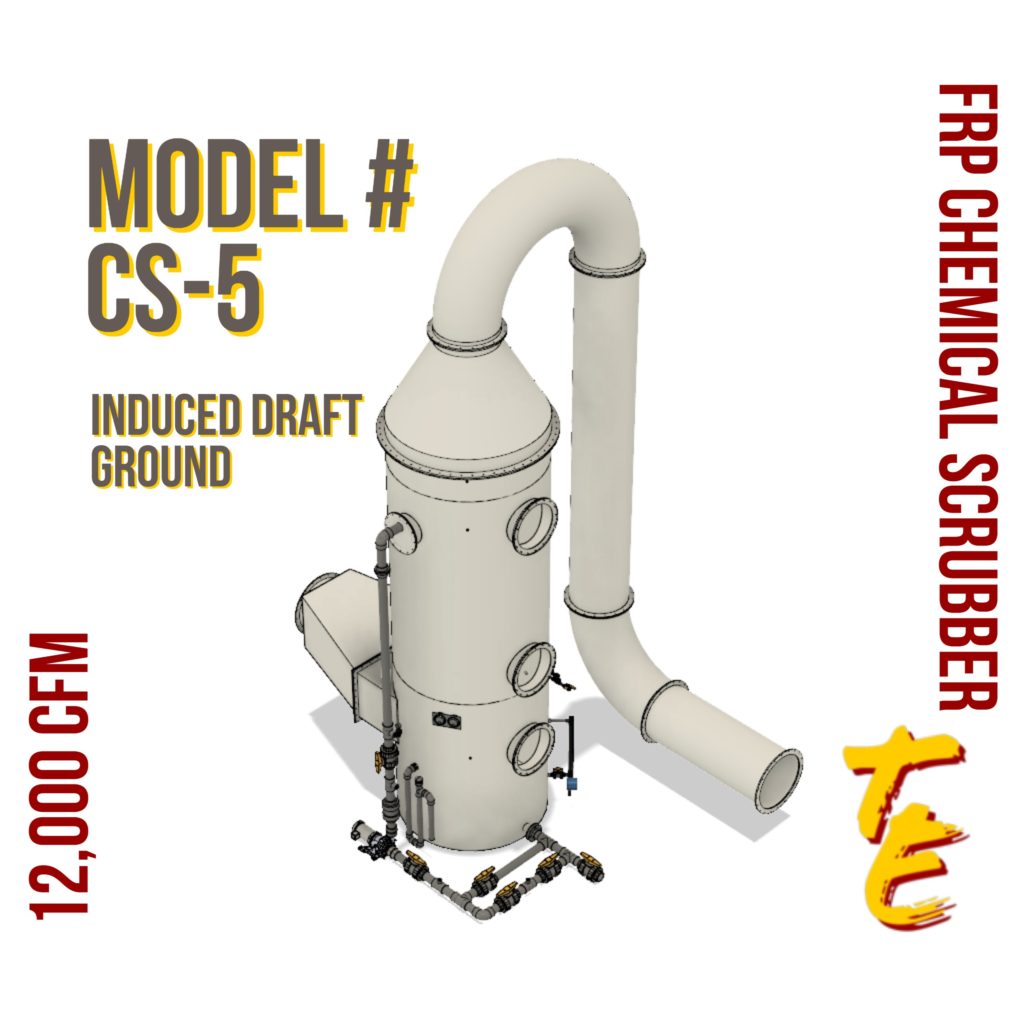
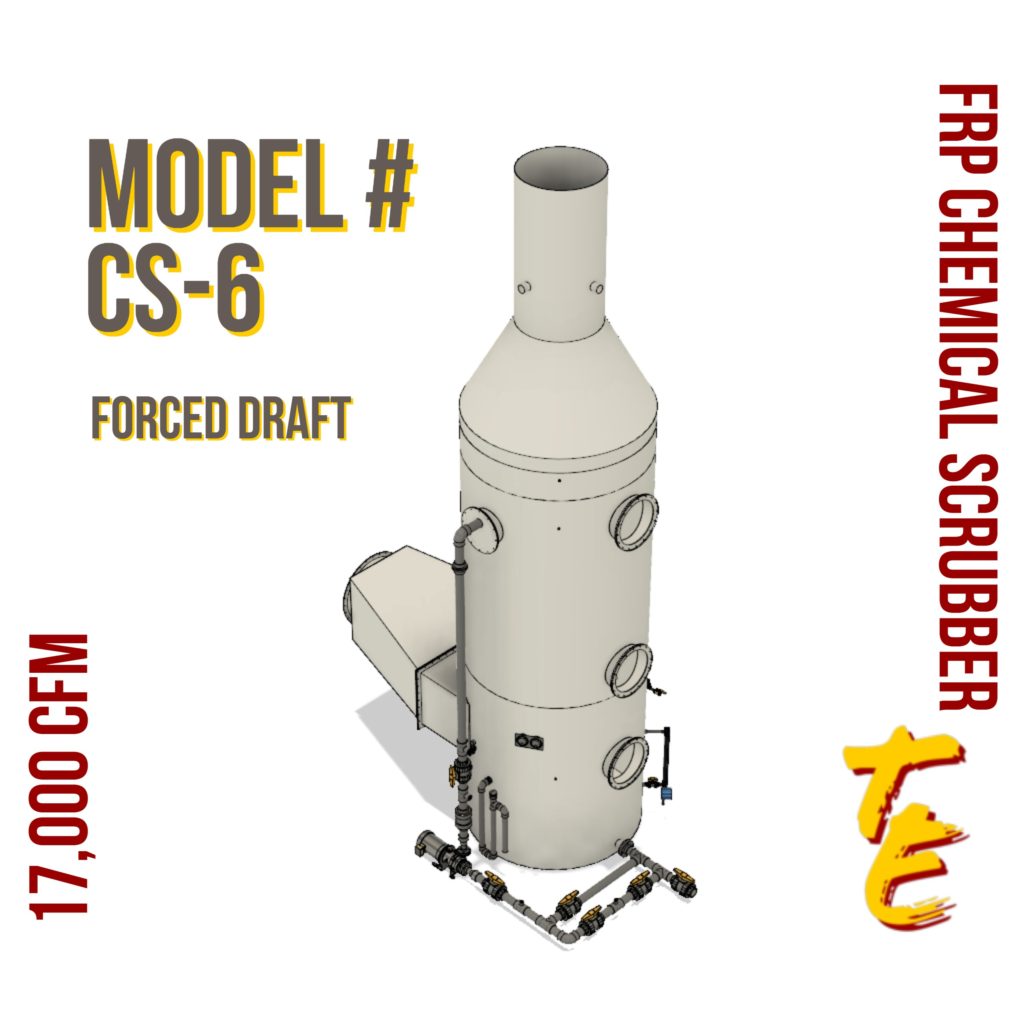
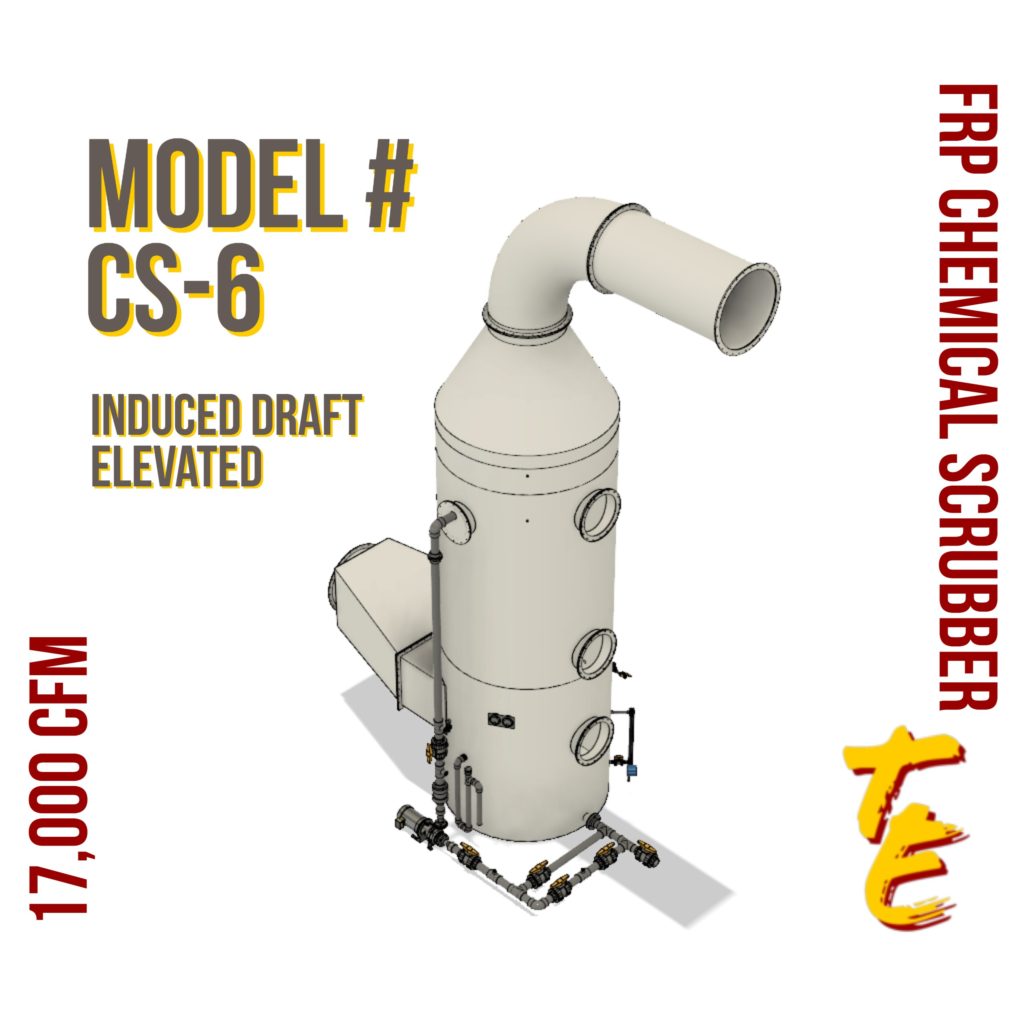
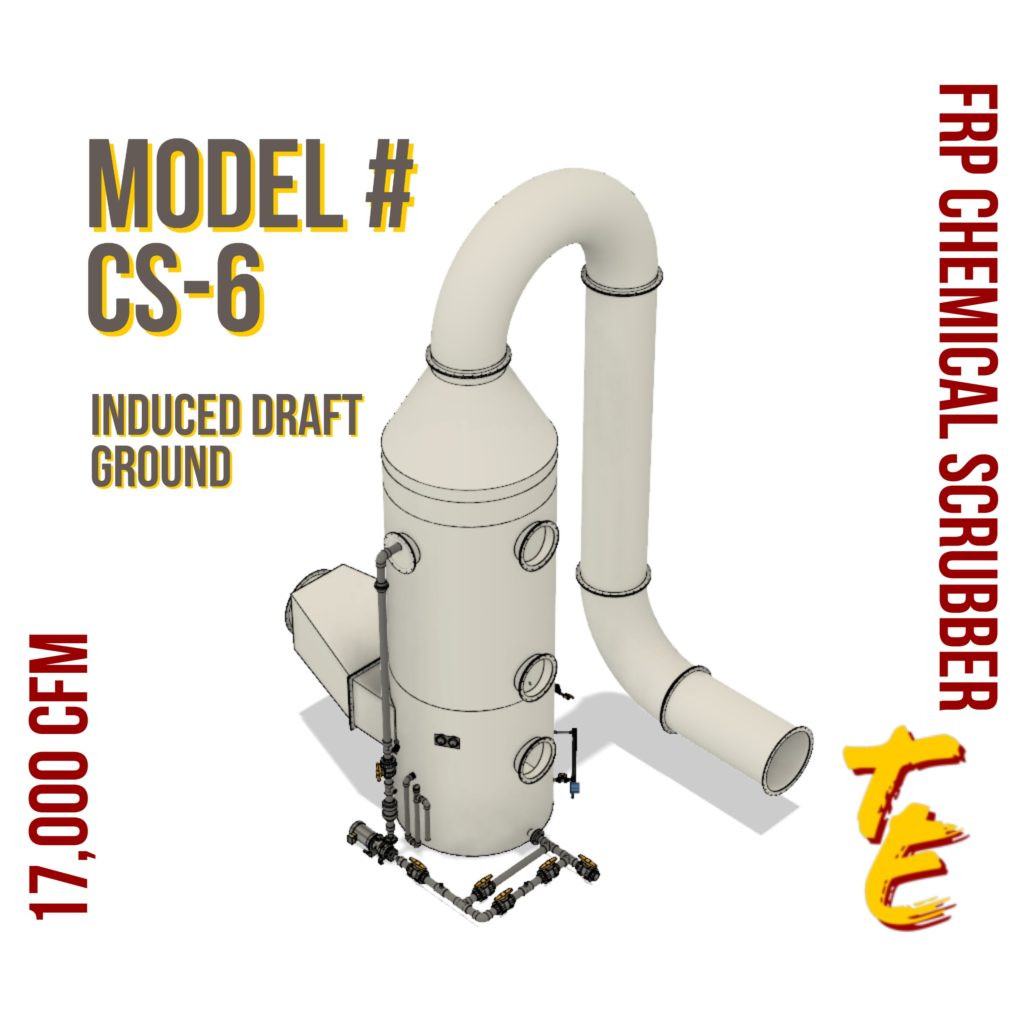
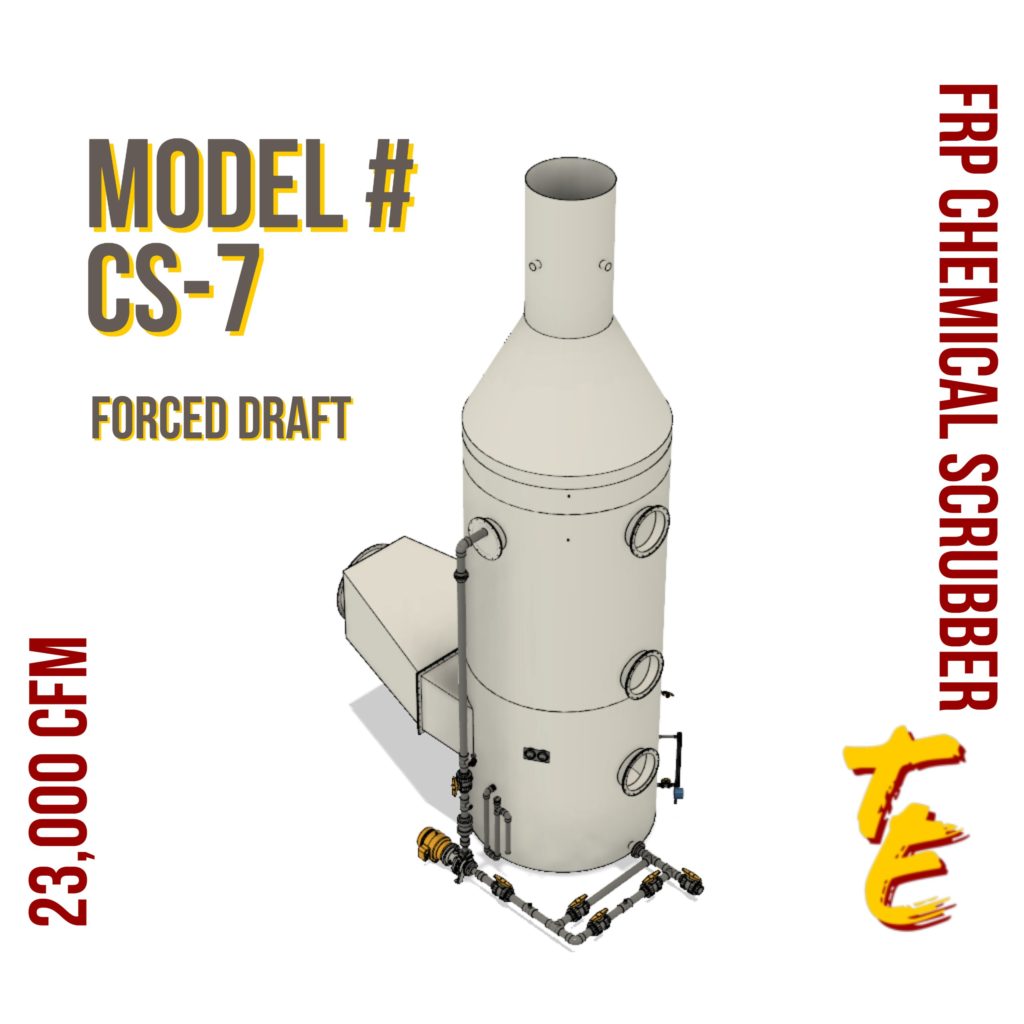
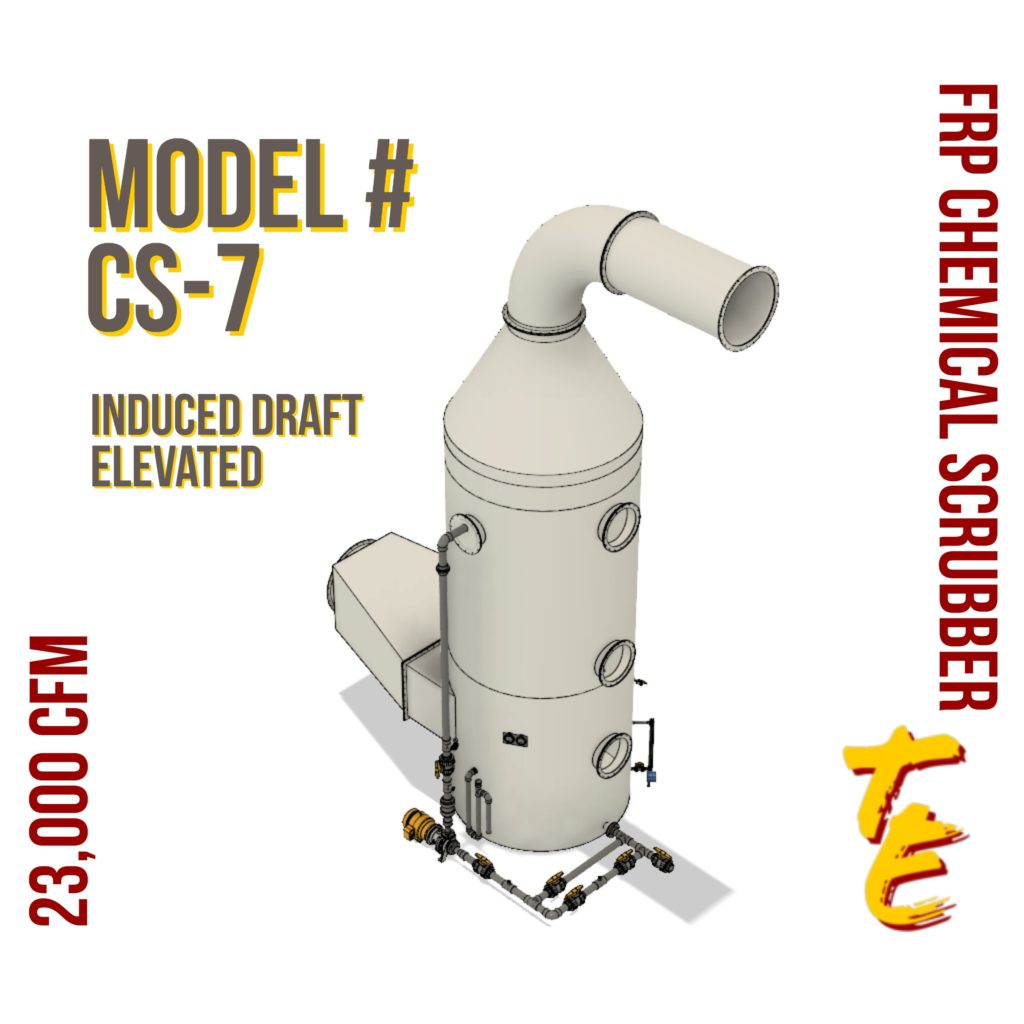
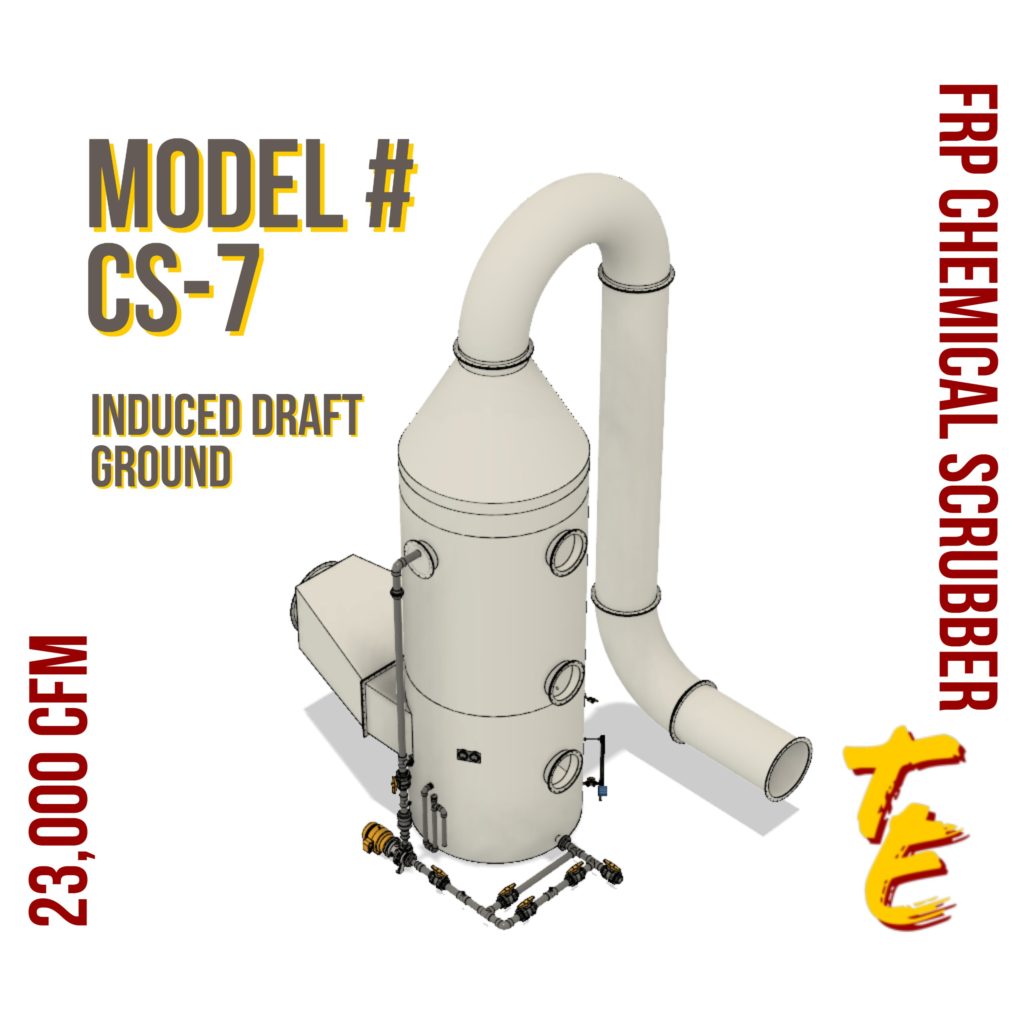
Chemical scrubber P&ID
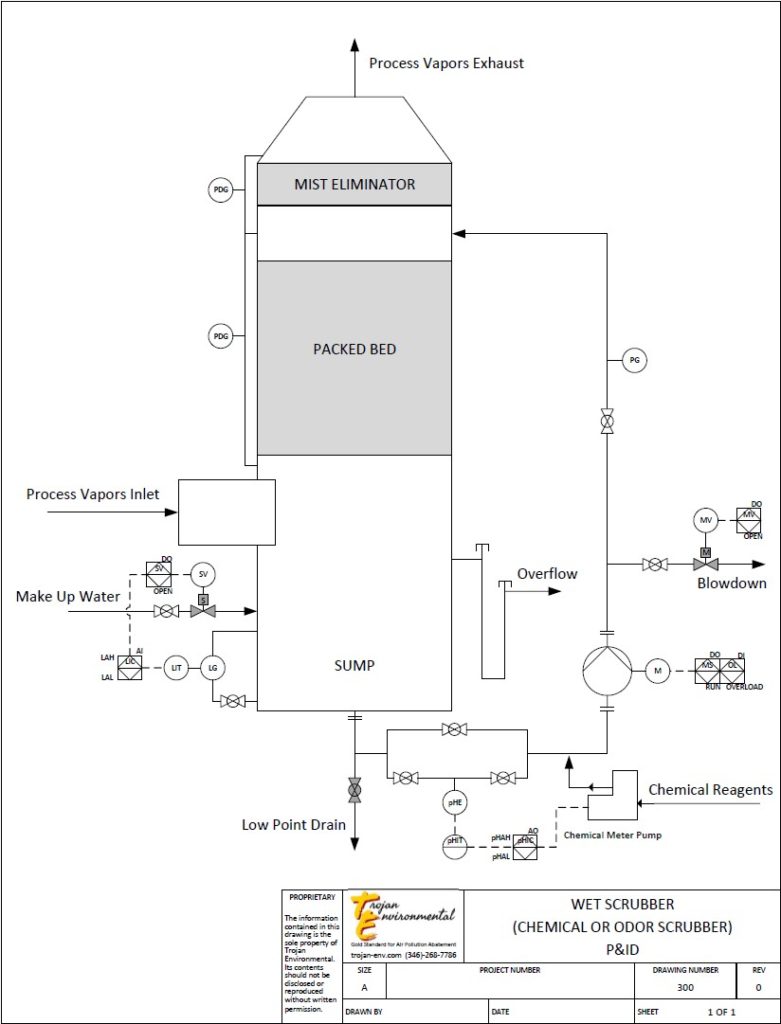