Principles of Operation
Venturi Scrubbers are engineered for the removal of particulate matter from a gas stream. While they may entrain some chemical fumes as a side benefit, the design focus are solid particulates. They are commonly constructed from Stainless Steel or FRP (Fiberglass Reinforced Plastic).
A Venturi Scrubbers’ removal efficiency is primarily a function of power. >99% removal efficiency at 2.0 microns is easily achieved. But for particulates sized below 0.5 microns, the power requirements for high removal efficiencies become excessive. Engineering calculations will physically size the equipment, determine the power (system fan specifications), water flowrate, and wastewater blowdown.
The injection header delivers the sump water to the top of the Venturi Scrubber and into the vapor stream. Spray nozzles creating small droplets for distribution are not necessary but can be used. A simple open pipe to deliver the water is also acceptable, as the downstream Venturi Throat will ensure proper distribution and mixing.
The process vapor stream, containing the particulates, enter into the Venturi Scrubber's inlet transition. This stream may have positive pressure applied and pushed into the Scrubber (Forced Draft) or may be under negative pressure and sucked into the Scrubber (Induced Draft). A forced draft fan arrangement is less ideal because the incoming particulate loading may build up or become a maintenance issue for the fan. With the induced draft arrangement, the particulates are already removed by the Scrubber before the vapor stream sees the fan.
The heart of the Venturi Scrubber is the Venturi Throat. The throat necks down to a smaller diameter, to increase the process vapor’s velocity. Water, from the injection header, also passes through the high velocity throat, which create small droplets. The higher the vapor velocity, the more shearing occurs on the water, and the smaller the droplets become. Tiny droplets are more effective than large droplets at mechanically impacting and entraining small diameter particulates.
Velocity through a pipe can be measured as pressure drop. Therefore, pressure drop, through the throat, is the main factor when sizing a Venturi Scrubber. Higher pressure drops, lead to higher removal efficiencies at smaller particulate diameters.
The sump is a reservoir of water, which feeds the system pump. The sump water will scrub the incoming particulate laden process, in the Venturi Throat, and entrain the solids. As water droplets exit the throat section into the larger diameter sump, velocities significantly slow down and the droplets fall into the liquid reservoir. Over time, the water becomes dirtier and more saturated with solids, which necessitates blowdown (discharge) to wastewater treatment. The rate or frequency of blowdown is dependent upon the incoming particulate loadings. Higher inlet particulate loadings lead to more blowdown.
Finally, the sump is very dynamic with water constantly being evaporated, some being sent to blowdown, and make-up water solenoids turning on/off, along with turbulence, possible foaming issues, or solids buildup. Therefore, to ensure proper operation of the sump and Venturi Scrubber, quality liquid level instrumentation is necessary.
The system pump should be sized accordingly for full liquid flow and static pressures needed to recirculate the sump water to the injection header. The pump should be verified compatible with any unique chemistries associated with the particulates being removed. Typically, the pump will just see recirculated water with low concentration particulates.
The clean vapor stream passes through the mist eliminator as the final section of the Scrubber. A composite mesh pad is an example of a mist eliminator, comprised of interwoven fibers built up in coarse and fine layers. Water droplets that are carried in the vapor stream, are impacted on this mesh pad. The clean vapor stream passes through, whereas large water droplets are collected on the mesh pad and allowed to drain back down.
The clean vapor stream exits the exhaust section of the Venturi Scrubber with the particulates removed down to requested emission limits. This cleaned vapor stream will be fully saturated with water (100% relative humidity). If the temperature of the vapor stream cools through additional ductwork, a stack, or as it exits into the atmosphere, water vapor will begin to condense out. That is why some exhaust stacks display a white water vapor cloud that quickly dissipates.
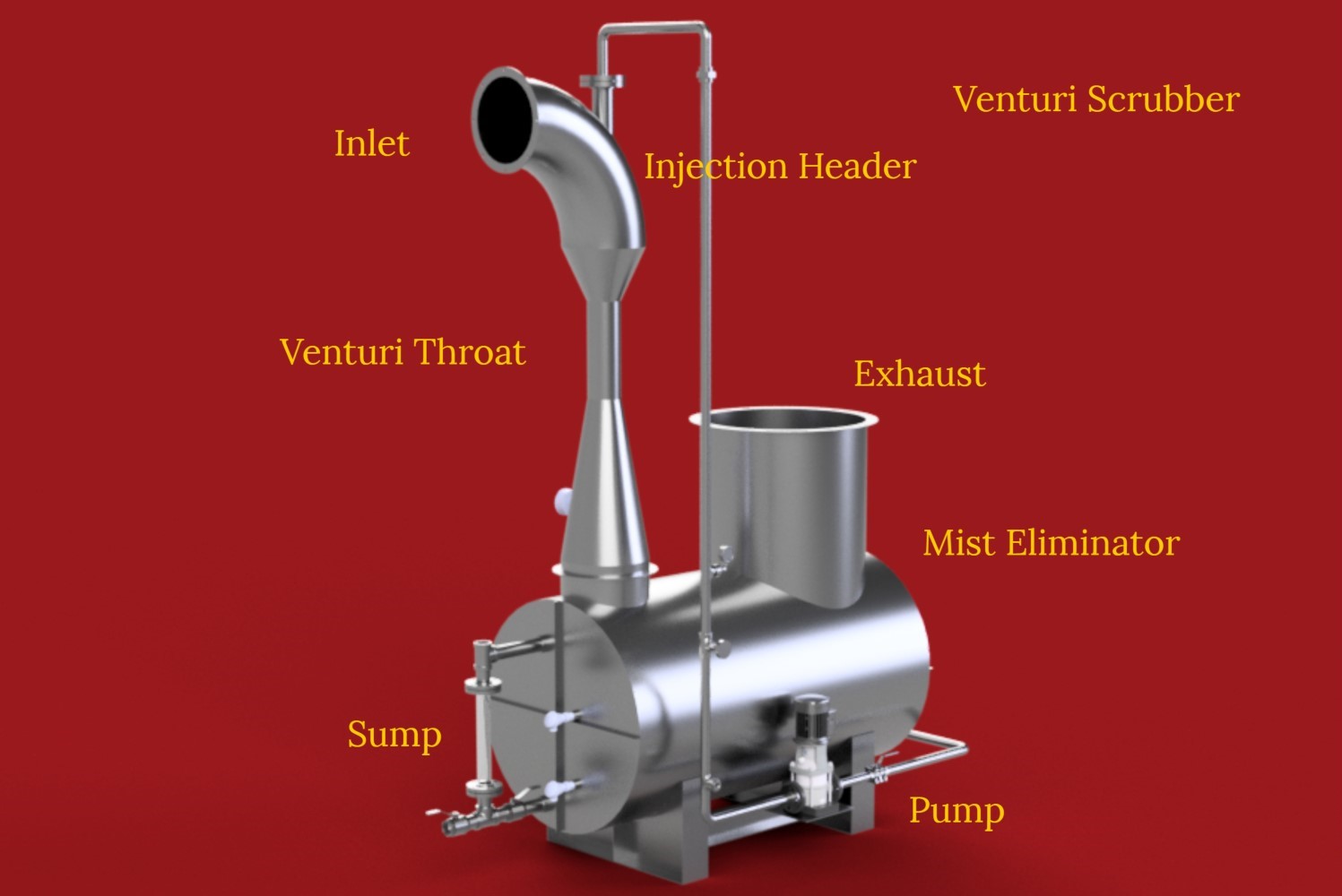
PM2.5 and PM10
- PM2.5 stands for Particulate Matter 2.5 microns in diameter or smaller. It is also known as fine particulates.
- PM10 stands for Particulate Matter sized between 2.5 microns and 10 microns in diameter.
- 1 micron is the same as 0.001 mm or can be written as 1 μm. The width of a human hair may average 70 μm. Therefore, the particulate pollution we are targeting is much smaller.
- The Clean Air Act includes PM2.5 and PM10 as part of their Criteria Air Pollutants. These particulates are harmful to human health because they can penetrate deep into the lungs, affecting the respiratory system. But there are numerous other health concerns associated with elevated and prolonged exposure to PM2.5 and PM10.
- Particulate Matter does occur naturally in our environment through various reactions in our atmosphere, forest fires, volcanoes, etc. But man-made pollution is evident by elevated PM concentrations in urban and industrial areas. The dirty haze one sees over some major cities is due to PM.
Particulate Size Comparison
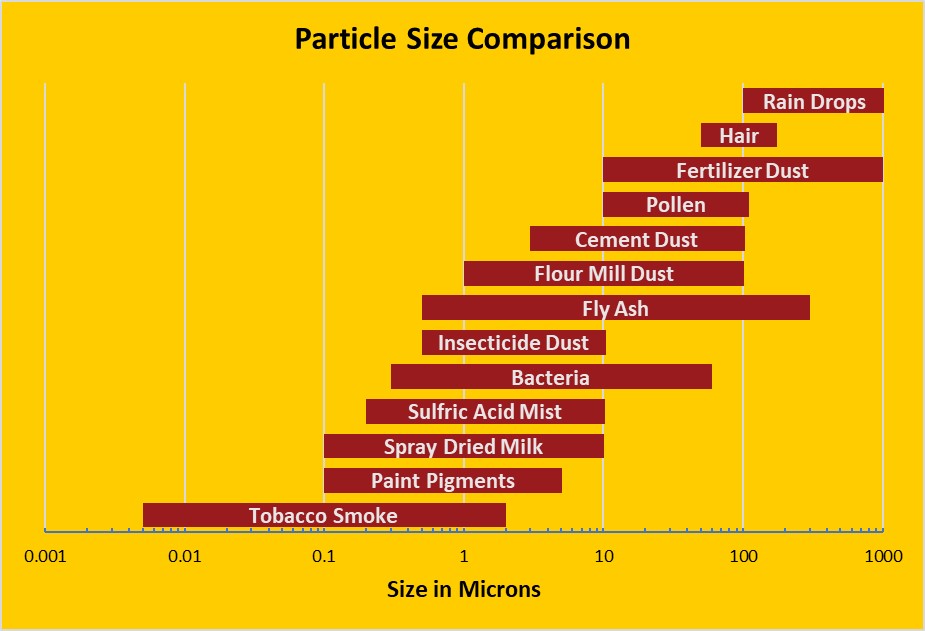
Venturi scrubber P&ID
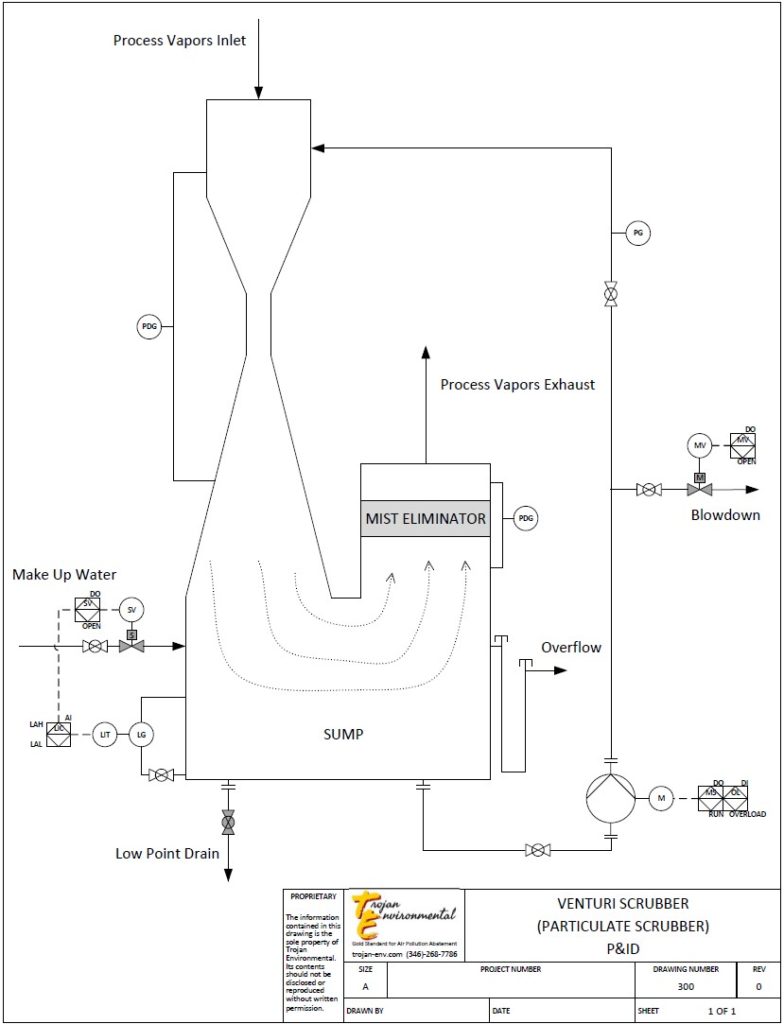
Vortex Venturi Standard Sizes
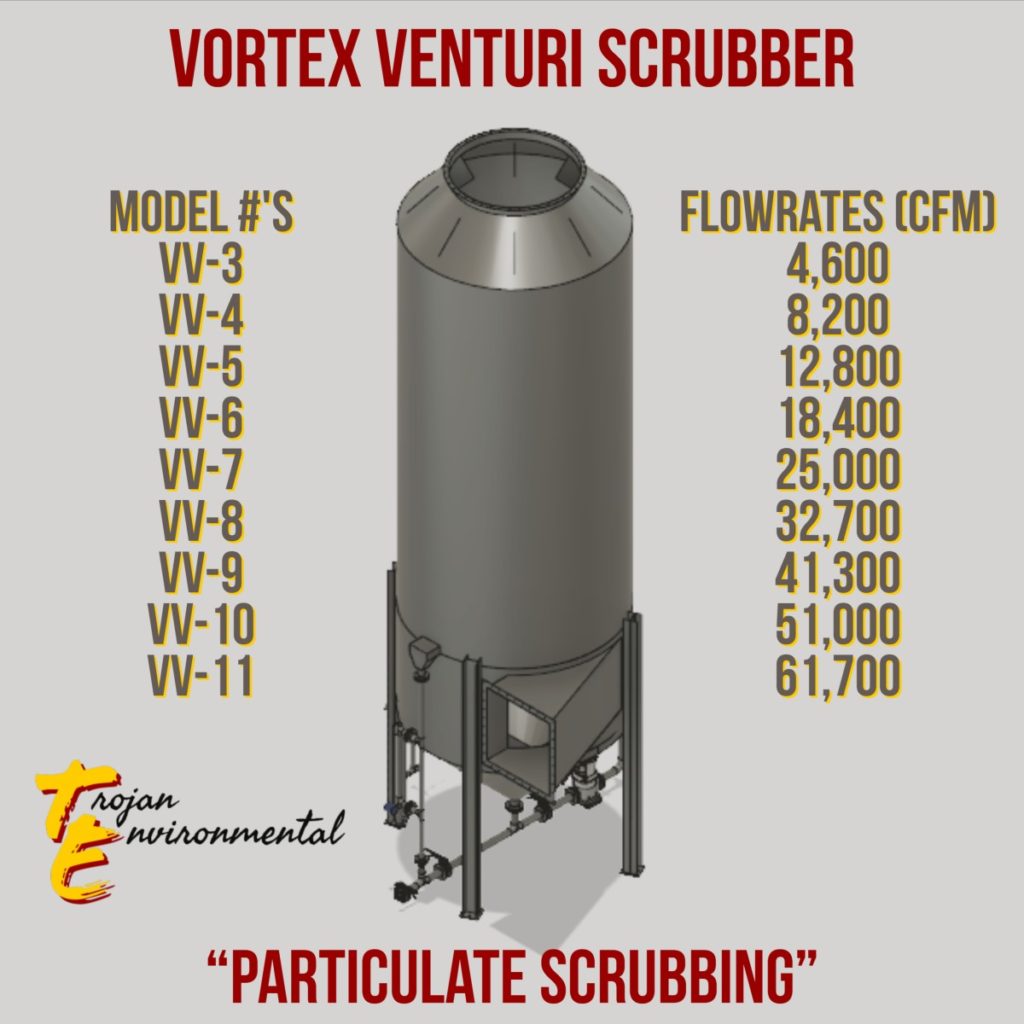
Vortex Venturi scrubber P&ID
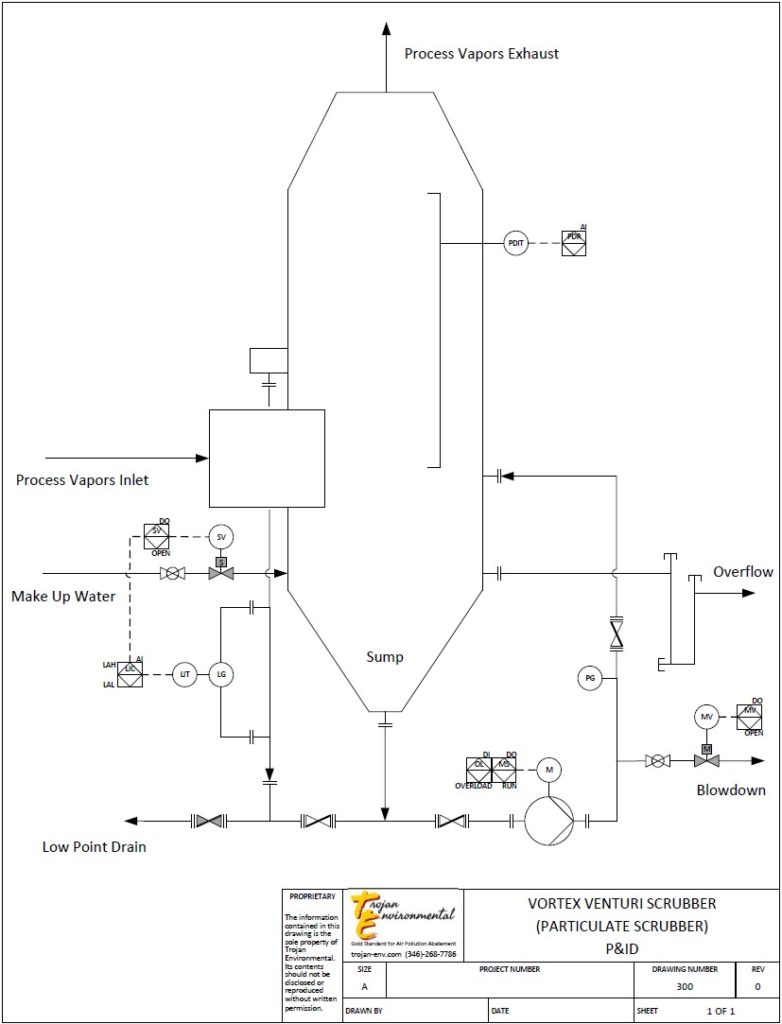